A quick search within the OSHA website to find requirements for the vet industry reveals…nothing. Well, not nothing, but it’s certainly not easy to find answers about how OSHA regulations impact our industry. Especially when you start looking deeper into specific topics like Safety Data Sheets.
As you know, safety data sheets (SDS) fall under the purview of the U.S. Department of Labor to ensure that Americans have safe and healthy work environments. As one part of the five key required elements in your Hazard Communication Program, you’ll need an SDS for every chemical and hazardous material in your practice. Fascinatingly, though, “lack of safety data sheets” remains number five on the list of the most commonly cited OSHA violations in the veterinary industry today.
This is where we can help! We gathered some of the most frequently asked questions from SDS webinars we’ve hosted, as well as from OSHA compliance courses offered through Patterson Veterinary University, and broke down the answers here! Below are your top 8 questions and answers.
1. Can we look up SDSs online, in lieu of a paper binder?
Technically, yes. To clarify, you can keep your forms digitally, but they can’t be housed behind any other barrier of entry, such as a password. Consider that hunting for safety data sheets online can be slow or time-consuming in safety situations that require speedy intervention.
Note: Most practices have an average of 300 products that require SDSs and OSHA requires them to be up to date from the last 30 years, regardless if the substance is still in your clinic.
2. What should I do if I’m having trouble locating a manufacturer’s SDS? Can I substitute with an equivalent? Are generic brand vs. brand name SDSs interchangeable since they have the same active ingredients?
If you have exhausted all other options in locating a manufacturer’s SDS, your last resort is to directly contact the manufacturer by phone or email to request they provide the SDS document.
Theoretically, generic and brand name products with the same ingredients should have nearly identical SDSs. There can be slight formulation differences, however, that would not make generic and brand name SDSs interchangeable. It is always best to use the SDS that directly corresponds to the product you have, from the manufacturer or supplier you got it from. Similarly, an SDS for an equivalent product should not be considered interchangeable.
3. Do I need to worry about SDS compliance if I’m a small, one-doctor practice?
Yes, OSHA compliance is legally required, regardless of the size or type of practice or facility location, whether single doctor, mobile, equine, etc.
4. Do the same rules apply to colleges? Do I need SDSs for the supplies that sit on veterinary students’ desks?
Yes. If you’ve purchased a product in bulk, and divided it into secondary containers – spray bottles, for example – each spray bottle requires its own label. Patterson’s AutoSDS software makes this easy. You just need some Avery labels and a printer.
5. How often do OSHA inspections happen?
OSHA doesn’t have a specific timeline for inspections. The frequency of inspections can vary depending on factors such as industry, types of hazards present, employee complaints, size of company and incident rates.
While low-hazard sites may experience inspections far less frequently than high-hazard sites, for example, an OSHA inspection can happen at any time, so it is important to maintain continuous compliance.
6. Are SDSs for medications and chemicals the same? What do the sheets look like?
No. safety data sheets for medications and chemicals are not the same. While they follow a similar standardized format, the specific content and details may cover different information based on the purpose and hazards associated with each.
Both medication and chemical SDSs cover identification, composition, handling procedures and health effects. But medications focus on medical use while chemical SDSs focus on safe industrial use as regulated by OSHA. The product labels also reflect a difference in purpose through the information highlighted.
7. Are there downsides to keeping an SDS binder?
While the vet industry has seen a broad shift towards paperless, digital solutions, many clinics still choose to manage their safety data sheets with a binder. This method can meet OSHA requirements, but it’s labor-intensive when done correctly and leaves room for human error.
Manufacturers regularly update their SDS materials so a practice would need to stay informed on changes to each sheet for hundreds of products to ensure they have the correct version. Plus, they’d need to archive and house older versions to meet the Employee Exposure Records requirement, even if the substance is no longer in clinic.
Another potential issue is that paper binders have a tendency to become scarce or hard to physically locate within the practice. This means it’s not a fast way to get safety information when the team needs it and doesn’t meet OSHA requirements for “readily available.” Be mindful of these pain points when deciding how to approach safety in your clinic, with your team.
8. Why did we create AutoSDS software?
Patterson saw how difficult and tedious it can be to remain compliant with OSHA standards, so we had software developed to keep track of, update and house these sheets. It’s called AutoSDS and your practice’s library houses SDSs for products you purchased, and the sheets are searchable within your library.
We work with manufacturers to keep the data current, so you don’t have to. Any of your new purchases are added automatically, and we can even import sheets from products not purchased from Patterson.
Three-ring binders are a holdover from days when we also used paper medical records. Everything is digital, and SDSs are now, too. Since OSHA requires that information be readily available, setting up a quick-access link on every computer or tablet in your practice makes the information readily available. Plus, it frees up anyone on your team from having to dedicate administrative time towards SDS upkeep, so you can focus on patients instead!
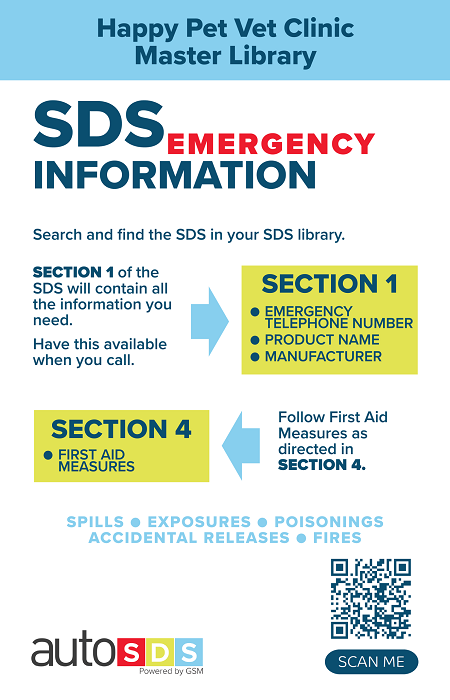
Share
Related blogs
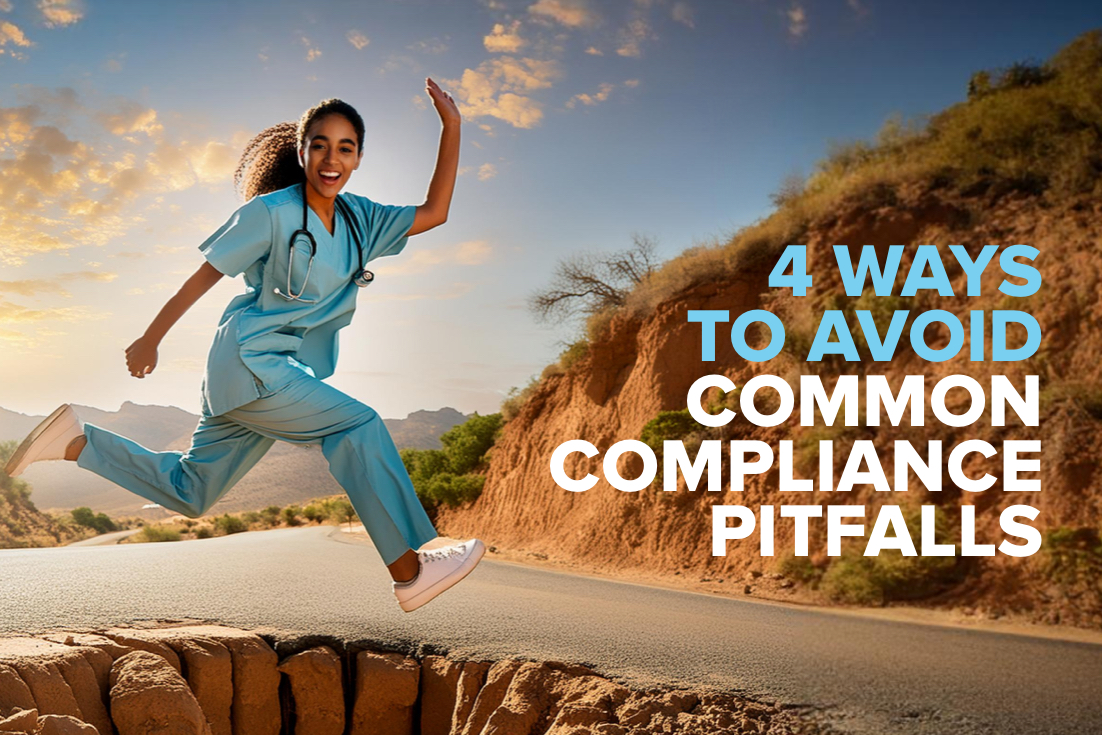
4 Ways to Avoid Common Compliance Pitfalls
We’ve got recommendations to help you avoid the most common OSHA compliance pitfalls and safeguard your employees’ health and wellbeing.
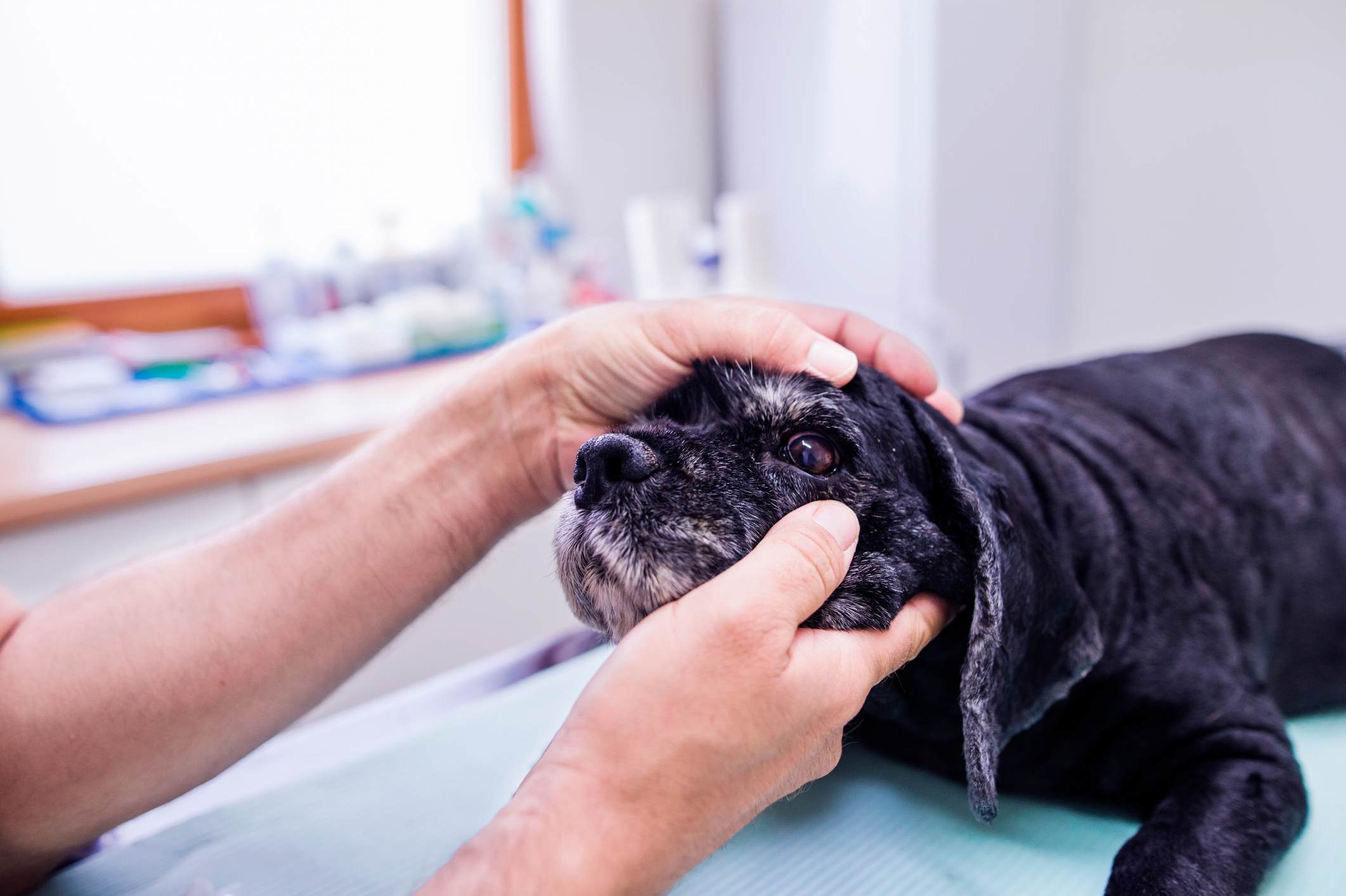
Revolutionizing Veterinary Ophthalmology: Enhancing Ocular Health with Innovative Tear Film Solutions
The eye is a marvel of nature, with its intricate structures working together to provide vision and protection. One crucial component that often goes unnoticed is the tear film, which acts as a hydration oasis for the eye. In this blog, we will delve into the layers of the tear film, its essential functions, causes of Dry Eye, causes of Corneal Ulceration, and the revolutionary solutions like BioHanceTM and Sentrx Animal Care Ophthalmology Products.